Abbattimento di emissioni contenenti inquinanti complessi
SETTORE
LA RIDUZIONE DELLE EMISSIONI DI INQUINANTI COMPLESSI RICHIEDE LA CONOSCENZA DEGLI INQUINANTI STESSI PER TROVARE UNA SOLUZIONE IN GRADO DI GESTIRLI. QUESTE SOSTANZE INCLUDONO COMPOSTI ORGANICI ALOGENATI, AZOTATI E CLORURATI.
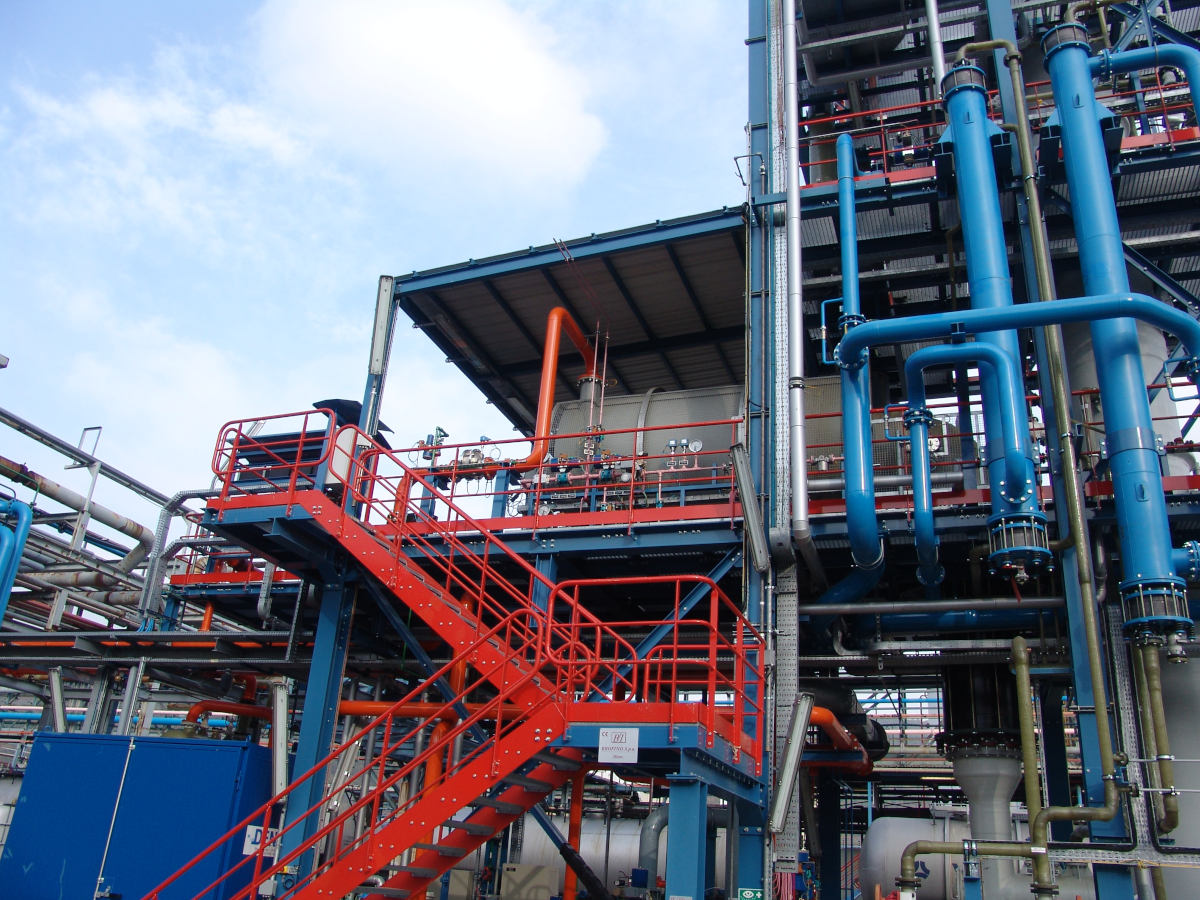
La presenza di alcune tipologie di inquinanti rende il trattamento delle emissioni atmosferiche più complicato, in quanto per ottenere il livello di depurazione richiesto è necessario considerare:
- parametri operativi specifici, per ottenere elevate rese di depurazione e limitare al massimo la formazione di sottoprodotti inquinanti
- la necessità di un ulteriore fase di trattamento, dedicata all’abbattimento degli inquinanti secondari eventualmente prodotti
- l’utilizzo di materiali resistenti a condizioni di esercizio gravose, sia in termini di temperatura, che in termini di resistenza alla corrosione
Un caso tipico è il trattamento di emissioni atmosferiche contenenti composti organici alogenati, che si riscontra nell’industria petrolchimica o farmaceutica.
L’IMPATTO AMBIENTALE DEI PROCESSI DI PRODUZIONE SOLVENTI CLORURATI
Le emissioni derivanti dai processi di produzione di dicloro etano e cloruro di metile, comprendono le emissioni provenienti dalle seguenti sezioni:
- clorazione diretta
- stoccaggio
- distillazione
- distruzione ipocloriti
- caricamento
Queste emissioni, essenzialmente costituite da azoto ed ossigeno, sono caratterizzate dalla presenza di idrocarburi aromatici (toluene, xilene) e composti organici clorurati (1,2 dicloroetano, cloruro di metile) oltre a cloro gassoso e acido cloridrico.
Le caratteristiche delle emissioni
Le emissioni atmosferiche derivanti dai processi di PRODUZIONE DICLORO ETANO possiedono le seguenti caratteristiche:
VARIABILE | CARATTERISTICHE |
---|---|
Temperatura | ambiente |
Presenza di composti organici volatili (C.O.V.) | Molto variabile, a partire da poche decine a centinaia di kg/h, con picchi |
Portata di emissione | (< 1500 Nm3/H) |
Ciclo di funzionamento | In continuo |
variabilità | Elevata, derivante dai processi discontinui (batch) che caratterizzano questo tipo di produzione |
OBIETTIVI DI DEPURAZIONE
L’obiettivo di depurazione è quello di ridurre al massimo l’emissione in atmosfera di inquinanti dannosi per l’ambiente (C.O.V.), degli acidi inorganici (HCl) generatisi nel processo di ossidazione, evitando la formazione di microinquinanti organici (diossine, furani)
LA SOLUZIONE ATTRAVERSO IL PROCESSO DI OSSIDAZIONE TERMICA E SUCCESSIVO ABBATTIMENTO AD UMIDO
Per risolvere la problematica ambientale, caratterizzata da emissioni con caratteristiche di estrema variabilità si in termini di portata d’aria emessa che di flusso di massa di inquinanti, è stato installato un impianto di ossidazione termica abbinato ad una torre di lavaggio ad umido.
L’ossidazione termica è la tecnologia più indicata per il trattamento di portate di emissione di lieve entità, molto variabile, in presenza di carichi organici molto variabili, in quanto consente un repentino adattamento alla variabilità dell’emissione garantendo condizioni di processo costanti.
L’abbattimento ad umido, con dosaggio di una base quale reagente, consente la neutralizzazione degli acidi inorganici prodottisi per ossidazione dei composti organici alogenati nel processo di combustione.
GLI ACCORGIMENTI INDIVIDUATI PER L’APPLICAZIONE NELL’INDUSTRIA DI PRODUZIONE SOLVENTI CLORURATI
L’OSSIDAZIONE TERMICA E L’ABBATTIMENRTO AD UMIDO SONO PROCESSI FREQUENTEMENTE UTILIZZATI IN COMBINAZIONE PER IL TRATTAMENTO DELLE EMISSIONI ATMOSFERICHE CONTENENTI INQUINANTI COMPLESSI, QUALI SONO I COMPOSTI ORGANICI ALOGENATI, LA CUI OSSIDAZIONE PUO’ GENERARE INQUINANTI INORGANICI DANNOSI PER L’AMBIENTE.
L’applicazione nell’industria petrolchimica ha dovuto prevedere l’individuazione e l’applicazione di specifici accorgimenti volti a consentire i seguenti obiettivi:
- L’ottenimento delle più elevate prestazioni di depurazione, attraverso uno specifico dimensionamento dei parametri di processo: temperatura di ossidazione >1.000 °C, tempo di permanenza in camera di combustione >1s, ossigeno residuo nei fumi depurati >3%
- L’utilizzo di materiali refrattari cementizi idonei a garantire costanti temperature di esercizio, nonostante la estrema variabilità dell’emissione da trattare
- Il repentino raffreddamento dell’emissione ossidata, grazie ad una sezione di quench, per evitare la formazione di microinquinanti organici
- L’utilizzo di materiali resistenti alla corrosione: grafite, hastelloy, e materiali plastici fibro-rinforzati per la sezione di abbattimento ad umido
I risultati ottenuti
I risultati ottenuti grazie all’abbinamento di queste tecnologie consentono di confermare la bontà della soluzione che ha permesso di conseguire i seguenti risultati:
- La durata dell’impianto nel tempo e la limitazione dei fenomeni corrosivi.
- L’ottenimento di valori di concentrazione di inquinanti in emissione in atmosfera ben al di sotto dei limiti normativi previsti, come rappresentato nella tabella seguente:
inquinante | u.m. | Valore garantito | Valore misurato-al collaudo |
---|---|---|---|
Acido cloridrico | mg/Nm3 | 10 | <1 |
Cloruro di vinile CVM + 1,2-dicloroetano DCE | mg/Nm3 | 1 | <0,5 |
Cloro Cl2 | mg/Nm3 | 5 | <0,3 |
Polveri totali | mg/Nm3 | 40 | Non rilevate |
Sostanze organiche volatili SOV | mg/Nm3 | 20 | 1 |
Metano CH4 | mg/Nm3 | 50 | <1 |
Ossidi di zolfo SOx | mg/Nm3 | 300 | Non rilevati |
Ossidi di azoto NOx | mg/Nm3 | 100 | 66 |
Monossido di carbonio CO | mg/Nm3 | 100 | <1 |
Diossine PCDD | ng/Nm3 | 0,1 | <0,01 |
Cloruro di etile EtCl | mg/Nm3 | 20 | <0,2 |